Introduction
Vibration testing is a crucial process in various industries such as automotive, aerospace, and electronics to ensure the reliability and durability of products under different operating conditions. One of the key components used in vibration testing setups is a diesel generator, which provides the necessary power to drive the shaker system that induces vibrations in the test specimen. In this article, we will explore the role of diesel generators in vibration testing, their key features, selection criteria, installation considerations, and maintenance best practices.
Role of Diesel Generator in Vibration Testing
A diesel generator plays a vital role in vibration testing setups by providing a reliable source of electrical power to drive the shaker system. The shaker system consists of an electrodynamic or hydraulic shaker that applies controlled vibrations to the test specimen. 150kw diesel generator for telecommunications towers simulate real-world conditions such as transportation, operation, or environmental factors to assess the structural integrity and performance of the product under test.
Key Features of Diesel Generators for Vibration Testing
1. Power Output: Diesel generators used in vibration testing setups are typically high-power units ranging from 50 kW to 1000 kW or more, depending on the size and capacity of the shaker system.
2. Load Capacity: Diesel generators should have sufficient load capacity to handle the peak power demands of the shaker system during vibration testing. They should also be able to provide stable and consistent power output to ensure accurate and repeatable test results.
3. Fuel Efficiency: Diesel generators designed for vibration testing should be fuel-efficient to minimize operating costs and reduce environmental impact. Features such as variable speed control and automatic load management can help optimize fuel consumption.
4. Noise and Vibration Levels: Diesel generators should be equipped with soundproofing and vibration isolation measures to minimize noise and vibration levels that could interfere with the testing process or affect the accuracy of test results.
5. Reliability and Durability: Diesel generators used in vibration testing environments should be highly reliable and durable to withstand continuous operation under demanding conditions. They should be equipped with robust components and built to industrial standards for long-term performance.
Selection Criteria for Diesel Generators in Vibration Testing
When selecting a diesel generator for vibration testing, several key factors should be considered to ensure compatibility and optimal performance:
1. Power Requirements: Calculate the total power requirements of the shaker system, including peak power demands, and select a diesel generator with adequate power output and load capacity.
2. Fuel Type: Diesel generators are commonly used in vibration testing setups due to their high power output, fuel efficiency, and reliability. Consider the availability of diesel fuel and the cost of operation when choosing a generator.
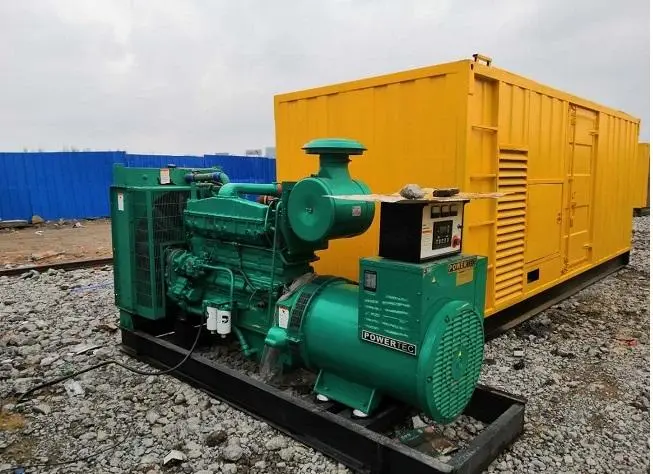
3. Size and Portability: Depending on the size of the testing facility and the mobility requirements, choose a diesel generator that is appropriately sized and portable for easy installation and relocation.
4. Noise and Emissions: Select a diesel generator with low noise and emissions levels to comply with environmental regulations and ensure a comfortable working environment for testing personnel.
5. Control and Monitoring Features: Look for diesel generators with advanced control and monitoring features such as remote operation, automatic shutdown in case of faults, and real-time data logging for better test management and safety.
Installation Considerations for Diesel Generators in Vibration Testing
Proper installation of diesel generators is essential to ensure safe and efficient operation in vibration testing setups. Consider the following installation considerations:
1. Location: Install the diesel generator in a well-ventilated and accessible location to facilitate maintenance and ensure proper cooling during operation. Keep the generator away from sources of heat, moisture, or vibration that could affect its performance.
2. Electrical Connections: Ensure that the diesel generator is properly connected to the electrical supply of the testing facility and the shaker system to prevent power interruptions and ensure reliable operation during testing.
3. Fuel Supply: Maintain a sufficient supply of diesel fuel and install a fuel storage tank with proper ventilation and safety measures to prevent spills or leaks that could pose a fire hazard.
4. Exhaust System: Install an exhaust system for the diesel generator to safely vent emissions outside the testing facility and comply with environmental regulations regarding air quality and pollution control.
5. Grounding and Safety: Properly ground the diesel generator to prevent electrical hazards and ensure the safety of testing personnel. Install safety features such as emergency shutdown switches and fire suppression systems for additional protection.
Maintenance Best Practices for Diesel Generators in Vibration Testing
Regular maintenance is essential to keep diesel generators in optimal condition and ensure reliable performance in vibration testing setups. Follow these best practices for diesel generator maintenance:
1. Routine Inspections: Conduct regular visual inspections of the diesel generator for signs of wear, damage, or leaks. Check the fuel system, cooling system, electrical connections, and exhaust system for any issues that could affect performance.
2. Oil and Filter Changes: Replace the engine oil and filters at recommended intervals to maintain proper lubrication and prevent engine wear. Use high-quality oil and filters compatible with the diesel generator model for optimal performance.
3. Cooling System Maintenance: Clean and inspect the radiator, cooling fans, and hoses regularly to prevent overheating and ensure efficient cooling of the diesel generator during operation.
4. Battery Maintenance: Check the battery condition, terminals, and electrolyte levels regularly to ensure reliable starting and operation of the diesel generator. Clean the terminals and apply corrosion-resistant coatings as needed.
5. Load Testing: Conduct periodic load tests on the diesel generator to verify its capacity and performance under various load conditions. Test the automatic voltage regulator (AVR) and governor system for proper operation and calibration.
Conclusion
Diesel generators play a critical role in vibration testing setups by providing the power needed to drive the shaker system and simulate real-world conditions for product testing. When selecting a diesel generator for vibration testing, consider factors such as power output, fuel efficiency, noise levels, reliability, and durability to ensure optimal performance and accurate test results. Proper installation and maintenance of diesel generators are essential to ensure safe and efficient operation in vibration testing environments. By following best practices for diesel generator selection, installation, and maintenance, testing facilities can achieve reliable and repeatable results in vibration testing applications.